-
Atlas Improvements
In the last 30 years, Atlas Foundry has invested strongly in its melt,
molding, sand and cleaning room equipment to position itself in a tough global
marketplace.
1985
- Atlas installed its first DISA Molding Machine. A DISAMATIC 2013 MK
IV A, rated at 400 molds per hour was installed increasing production capacity
to meet customers demands.
- This molding machine has an automated core setter to set the cores in the
mold; and an automatic pouring system.
- A pattern plate size of 18.9"X23.6" is accepted.
- Disamatic Molding machine.

1991
- In 1991, Atlas installed an Forty Ton ABB Induction Hold Furnace.
1996
- Atlas installed (2) Four metric ton Inductotherm Melt Furnaces. The
two new Inductotherm induction melt furnace have state of the art controls and
charging accessories.
1997
- Atlas increased its Core Room Production and storage
1999
- Atlas installed a DIDION Rotary Media Drum which results in cleaner
castings greatly reducing shot blast time and reducing labor in the knockout
and finishing department. This also results in clean remelt material
reducing slag at the furnace.
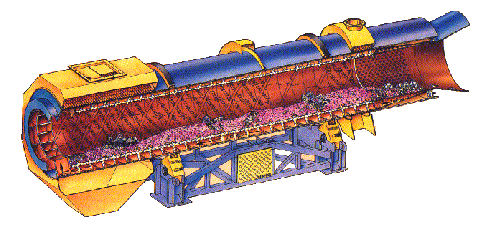
- Atlas also installed a Wheelabrator Mesh Blast Machine in 1999.
2000
- Atlas installed a second DISA. A DISAMATIC 2013 MK5-X Molding
Machine rated at 400 molds per hour.
- This molding machine has an automated core setter to set the cores in
the mold; and an automatic pouring system.
- A pattern plate size of 21"x29.5" is accepted.
2002
- Atlas Foundry Received its ISO 9001:2000 Certification
- As a committment to delivery quality castings, on time to its customers, Atlas Foundry pursued the ISO 9001:2000 objective, and received Certificaiton
2004
- Atlas Foundry redesigned and modernized the cleaning room / finishing department.
- Installed a system of conveyors and chutes to deliver castings to the grinding and finishing cells to improve efficiency
- Installed a Continous Blast Machine
- Castings are fed into and the Continous Blast and exit the blast without the need for an operatior to handle the casting
2009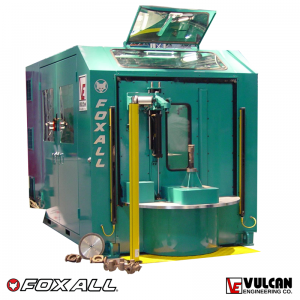
- Atlas installed a FoxallŽ 424FS Finishing Cell - Robotic Grinder from Vulcan Engineering
- The FoxallŽ 424FS Finishing Cell provides fast, reliable, consistent product finishing.
- FoxallŽ is a Foundry Protection package Robot.
- The robot gives maximum accessibility to the casting, with precise control giving a consistent quality finished product. Process consistency provides significant reduction in scrap rates.
2010
- Atlas installed a second FoxallŽ 424FS Finishing Cell - Robotic Grinder from Vulcan Engineering
2015
- Atlas made an investment for the future and replaced our first DISAMATIC 2013 MK IV A installed in 1985 with a new DISA 131-A MOULDING MACHINE.
- This molding machine has an automated core setter to set the cores in the mold; and an automatic pouring system.
- A pattern plate size of 18.9"X23.6" is accepted.
2016 and into the Future